1. Importance of Leak Testing for Reverse Lights
Although reverse lights are relatively small components, their sealing performance is critical for vehicle safety and user experience. As essential rear signal lights typically exposed at the vehicle's rear edge, poor sealing may lead to the following issues:
Method No. | Method Name | Principle | Advantages | Application |
---|---|---|---|---|
1 | Differential Pressure Method | Pressurizes the light housing and monitors internal pressure drop | Low cost, fast testing | Small, structurally regular reverse light assemblies |
2 | Mass Flow Method | Detects internal leakage flow using mass flow sensors | High precision, stable, suitable for automation | High-precision requirements or LED circuit-equipped reverse lights |
3 | Helium Leak Detection (Optional) | Identifies micro-leaks during R&D or for premium models | High cost, typically for verification phases |
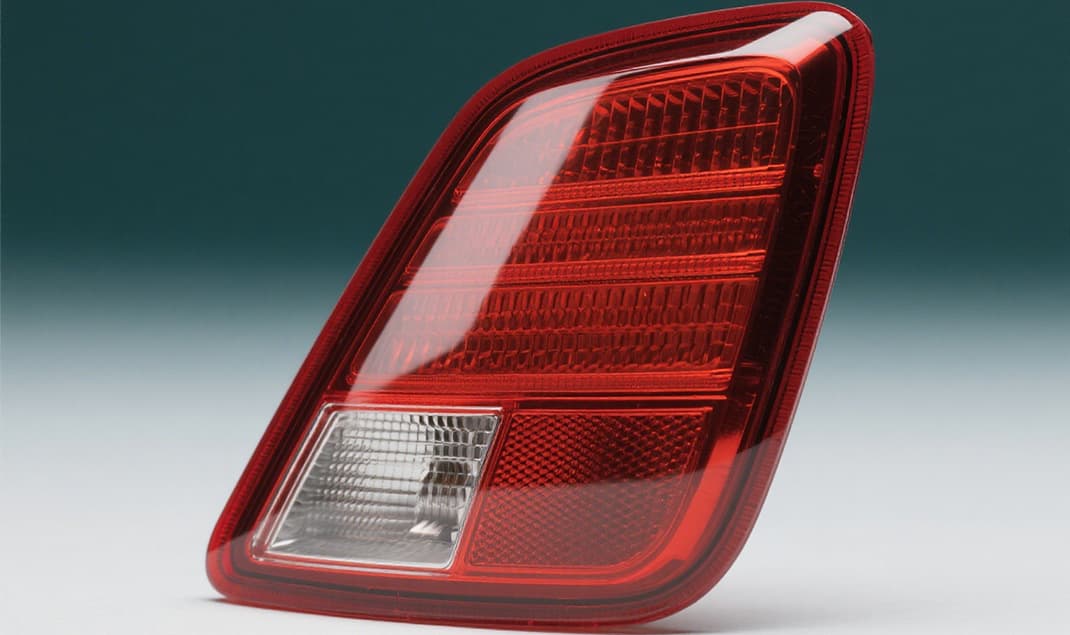
In 2022, a domestic automotive lighting manufacturer supplying Japanese brands encountered "water ingress in reverse lights during rain" complaints during initial mass production. Analysis revealed micro-leaks at injection-molded housing seams that traditional manual water testing missed. The manufacturer urgently implemented high-precision leak testers using mass flow method for 100% seal testing, successfully resolving the issue and passing Japanese client audits.
2. Common Leak Testing Methods for Reverse Lights:
Method No. | Method Name | Principle | Advantages | Application |
---|---|---|---|---|
1 | Differential Pressure Method | Pressurizes the light housing and monitors internal pressure drop | Low cost, fast testing | Small, structurally regular reverse light assemblies |
2 | Mass Flow Method | Detects internal leakage flow using mass flow sensors | High precision, stable, suitable for automation | High-precision requirements or LED circuit-equipped reverse lights |
3 | Helium Leak Detection (Optional) | Identifies micro-leaks during R&D or for premium models | High cost, typically for verification phases |
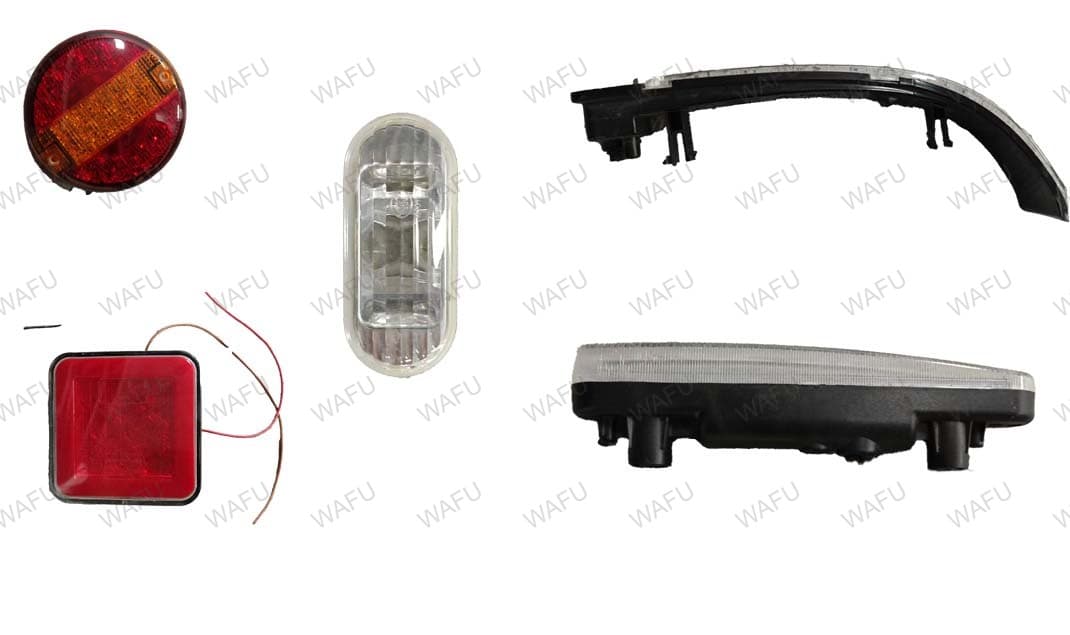
3. Leak Tester Operation Procedure (Mass Flow Method Example)
Step No. | Specific Procedure |
---|---|
1 | Fixture Loading: Place reverse light in dedicated sealing fixture |
2 | Sealing Closure: Close fixture to hermetically seal light housing |
3 | Pressurization: Inject gas at set pressure (e.g. 50-150kPa) |
4 | Pressure Stabilization: Maintain pressure for 2-3 seconds |
5 | Leak Detection: Measure flow rate in sccm (standard cubic centimeters per minute) |
6 | Pass/Fail Judgment: Compare against threshold (e.g. 0.3 sccm) |
7 | Result Output: MES system integration for data traceability and batch management |
Reverse light leak testing is essential for ensuring waterproofing, dustproofing, and signal reliability. Implementing high-precision leak testers represents the standard approach for delivering quality lighting products.
Recommended Products