Hermetic Electrical Connectors
In the aerospace industry, hermetic electrical connectors are responsible for signal transmission and power delivery between critical electronic equipment. These connectors must maintain absolute airtightness under extreme conditions—including vacuum, drastic temperature changes, and intense vibration. Any minor leakage can lead to: Oxygen and moisture intrusion causing circuit corrosion Gas escape in a vacuum environment leading to dielectric breakdown Condensation due to sudden temperature changes Reduced overall system reliability, threatening the safety of aerospace missions
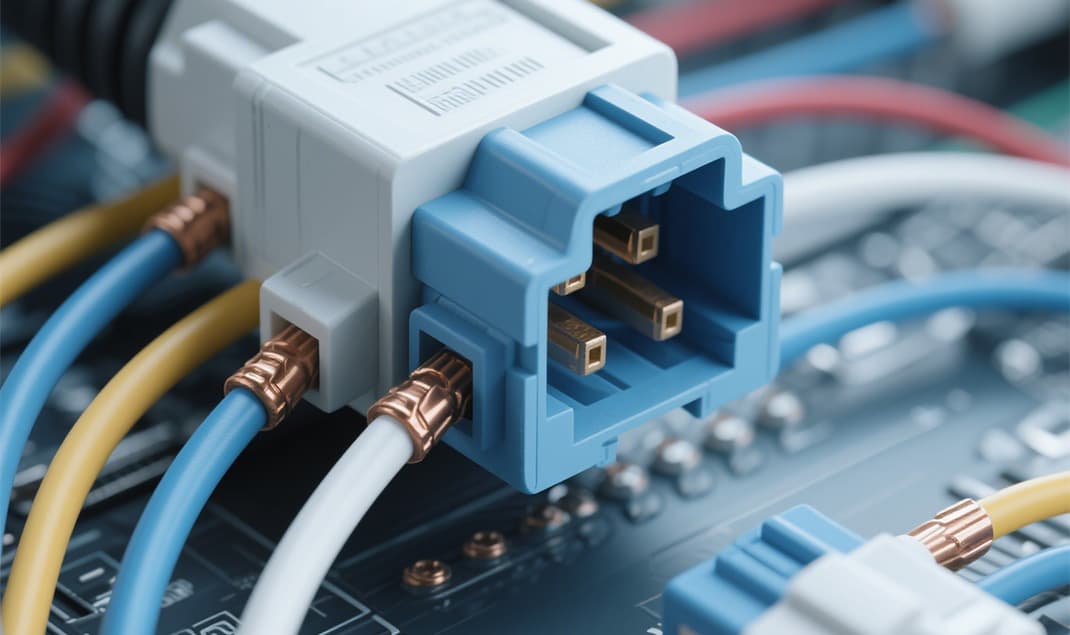
According to NASA statistics, approximately 15% of electronic system failures are directly related to connector seal failures, making leak testing a mandatory inspection item for aerospace-grade connector production.
To meet the stringent requirements of aerospace connectors, we provide a three-tier detection system. Below is a detailed professional testing solution:
Detection Level | Detection Method | Detection Sensitivity | Test Time | Applicable Stage |
---|---|---|---|---|
Production Line Rapid Screening | Pressure Differential Method | 1×10⁻⁴ cc/s | < 30 sec/unit | Full inspection on production line |
Precision Detection | Helium Mass Spectrometry Accumulation Method | 1×10⁻⁶ cc/s | 2-5 min/unit | Sampling inspection, full inspection for critical models |
Ultimate Detection | Helium Mass Spectrometry Vacuum Chamber Method | 1×10⁻⁹ cc/s | 10-15 min/unit | Type testing, first-article inspection |
Typical Testing Process Demonstration
Taking a D-sub hermetic connector for satellites as an example:
Testing Stage | Specific Steps |
---|---|
Preprocessing Stage | Automatic scanning to obtain product information |
Automatic adjustment of fixture to corresponding configuration | |
System self-calibration (including zero calibration, leakage rate baseline calibration) | |
Clamping Stage | Operator places the test piece |
Hydraulic sealing mechanism automatically engages (controllable pressure range: 5-50N·m) | |
Optical alignment system confirms proper clamping | |
Testing Stage | System automatically selects preset program (based on MIL-DTL-38999 standard) |
Performs three pressure cycle tests (-100kPa to +200kPa) | |
Real-time monitoring of pressure decay curve | |
Judgment Stage | System compares measured data with standard curve |
Automatically generates test report (including pressure curve, leakage rate, test conclusion) | |
OK units laser marked, NG units trigger audible and visual alarms |
Recommended Products